Prática da manutenção preventiva proporciona uma série de benefícios, como o funcionamento dos ativos em sua capacidade original; maior eficiência energética dos equipamentos; cumprimento dos prazos e maior segurança dos trabalhadores.
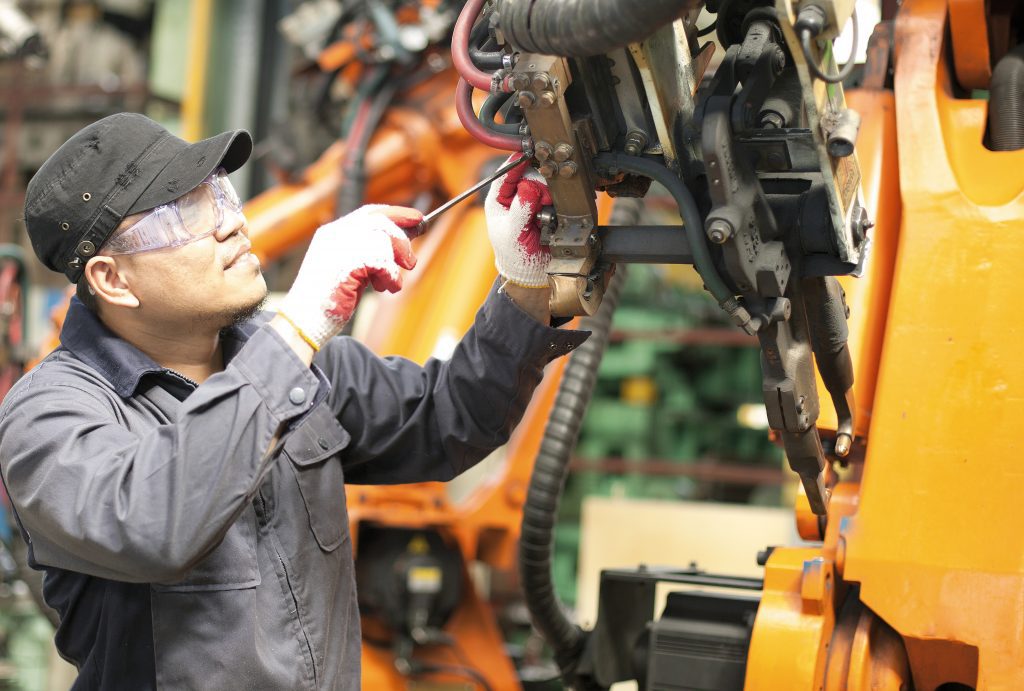
Tudo na vida precisa de cuidados especiais para surgir, se desenvolver adequadamente e prosperar. É o caso do corpo humano, das plantas e até dos relacionamentos, para ficar em apenas três exemplos aleatórios. Respectivamente, sinais como dores, falhas no crescimento e convivência ruim podem ser entendidos como alertas de que é preciso dedicar mais atenção a si próprio, àqueles que nos cercam e aos demais elementos presentes no cotidiano.
Na esfera profissional acontece algo parecido. Tomando como exemplo uma indústria qualquer, os cuidados devem ser direcionados para bens como máquinas, equipamentos, ferramentas, veículos e às próprias edificações, sistemas esses que estão sujeitos a ocorrências que vão do mau funcionamento a desgastes e quebras.
O atual mercado competitivo exige providências que vão além da antiquada mania de correr para consertar algo depois que ‘der problema’. O investimento em procedimentos de caráter preventivo se tornou vital para o adequado funcionamento de uma empresa, seja ela uma grande fábrica ou uma modesta oficina.
A tendência é se antecipar aos distúrbios mais frequentes, adotando a manutenção periódica como forma de evitar paradas não previstas, garantindo dessa forma a continuidade e o ritmo do trabalho e a consequente geração de receita.
Outro benefício que pode ser citado é obviamente mais importante do que qualquer patrimônio material: o bem-estar do homem. Além de ajudar a manter os negócios em funcionamento pleno, o adequado gerenciamento dos ativos fixos é importante também para garantir a segurança no ambiente de trabalho.
Mas não se pode deixar que a ânsia para aproveitar as potenciais vantagens inerentes à manutenção sobrepuje a razão. O sucesso da boa conservação dos bens de uma empresa depende do planejamento certo, respeito às normas técnicas e o destacamento de profissionais especializados.
Na indústria, em particular, é comum a prática de três tipos de manutenção, como detalha Victor Fagundes, promotor técnico em Automação e NR-12 da Reymaster Materiais Elétricos, distribuidora com sede em Curitiba (PR).
A manutenção corretiva tem caráter emergencial e serve para correção e substituição de componentes que atuam quando a falha já aconteceu. A manutenção preditiva é baseada na condição, analisada a partir da inspeção dos componentes das máquinas, para a detecção de possíveis falhas. A partir disso, gera-se um relatório, que aponta as possíveis falhas e sinaliza as melhorias necessárias a serem realizadas.
Já a manutenção preventiva (que será o foco desta matéria) é feita para reduzir ou evitar possíveis falhas, assim como aumentar o desempenho de máquinas e equipamentos. Normalmente é estruturada e planejada com base nos históricos das ocorrências ou em relatórios determinantes fornecidos pelos fabricantes.
Conforme destaca Emanuel Barcarolo, gerente de Engenharia do Grupo MH, todos os equipamentos que fazem parte dos sistemas civis, elétricos, mecânicos e térmicos precisam passar por manutenção preventiva, pois as normas, os fabricantes e as boas práticas recomendam essa atividade.
Para começo de conversa, é preciso planejar o trabalho a ser executado. “Para atingir um elevado nível de performance, se faz necessária a implantação de um plano de manutenção com análise de utilização e riscos, com o uso de ferramentas adequadas de gestão”, orienta Barcarolo.
Quanto ao time de manutenção, propriamente dito, é preciso reunir uma equipe que tenha passado por treinamentos, por exemplo, junto aos fabricantes dos equipamentos ou empresas especializadas. Os principais profissionais habilitados e capacitados para essa atividade são os engenheiros responsáveis; técnicos da área; técnicos de Segurança do Trabalho e oficiais de manutenção. “Para a realização de manutenções se faz necessário um grande aparelhamento, com equipamentos de alta performance e pessoal altamente especializado e treinado, além de dispor de equipamentos de proteção individual e coletivos específicos para cada atividade, demandando um alto investimento”, adianta Eduardo Mendes, CEO do Grupo MH, que atua há mais de 25 anos no mercado de infraestrutura.
Já as ações a serem empregadas dependerão do tipo de equipamento e dos riscos que ele oferece, no caso de parada. “Normalmente são utilizados checklists com os itens a serem verificados, como inspeções visuais, testes de performance, lubrificação e trocas programadas”, exemplifica Aníbal Facchini, gerente de Produção da Full Gauge Controls, fabricante brasileira de instrumentos para refrigeração, climatização e aquecimento.
No caso de subestações de energia, os trabalhos podem incluir inspeção termográfica, inspeção por ultrassonografia, análises físico-químicas e cromatográfica de óleos isolantes, resistência de isolamento, resistência de aterramento, resistência de contatos de dispositivos de manobra, relação de transformação, aferição dos relés de proteção, inspeção visual, limpeza, reaperto das conexões elétricas de potência e comando, testes funcionais e lubrificação, entre outros.
Nos painéis elétricos, devem ser feitas inspeções termográfica e visual, limpeza, reaperto das conexões elétricas, medição de grandezas elétricas utilizando analisadores de energia, medição de resistência de contatos em dispositivos de manobra e proteção, resistência de isolamento, aferição dos relés de proteção e teste funcional, entre outros.
Equipamentos térmicos, por sua vez, precisam passar por teste hidrostático, inspeção visual, limpeza, inspeção por ultrassonografia, reaperto de conexões, medições de eficiência energética e teste funcional, entre outros.
Eduardo Mendes alerta que cada área e/ou equipamento específico possui normas adequadas que orientam o trabalho de manutenção. A atividade pode ser regida por Normas Regulamentadoras (NRs) do Ministério do Trabalho e Emprego e por normas da ABNT (Associação Brasileira de Normas Técnicas). A NR-10, por exemplo, regulamenta as atividades relacionadas ao sistema elétrico, enquanto que a NR-13 regulamenta as atividades em caldeiras, vasos de pressão e tubulação. São exemplos de normas técnicas a ABNT NBR 5674 – Manutenção de edificações – Requisitos para o sistema de gestão de manutenção, a NBR 14039 – Instalações elétricas de média tensão de 1,0 kV a 36,2 kV e a ABNT NBR 5462 – Confiabilidade e mantenabilidade.
Benefícios da manutenção
De maneira geral, a adoção de um programa de manutenção preventiva visa garantir a vida útil dos equipamentos e sistemas, zelar pela vida dos colaboradores da empresa, evitar multas e estar de acordo com as normas vigentes.
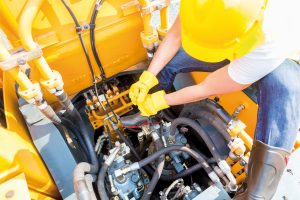
“Podemos dizer que entre os principais benefícios estão manter os ativos funcionando com a capacidade original, diminuir o risco de paradas por quebras, possibilitar o planejamento das manutenções corretivas e a aquisição de peças de reposição previamente, além de cumprir os prazos estabelecidos”, complementa Aníbal Facchini, gerente de Produção da Full Gauge Controls.
A realização de manutenção preventiva adequada em uma indústria pode também contribuir para maior eficiência energética dos equipamentos e de uma planta como um todo, pois, com redução do gasto energético se obtêm melhores resultados nos processos diretos e indiretos envolvidos com o ativo em questão.
A maior segurança no ambiente é outra vantagem proporcionada. Afinal, equipamentos trabalhando dentro de suas características nominais elevam seu desempenho, mitigando riscos de falhas e quebras e evitando acidentes de trabalho, propiciando ainda melhor conforto térmico e ajudando a preservar o meio ambiente.
O interessante das manutenções preventivas, observa Eduardo Mendes, é que essa atividade permite antever problemas e paradas, mitigando assim interrupções nos serviços de cada estabelecimento, seja ele um data center, hospital, unidade fabril ou instituição de ensino. “Muitas vezes, as empresas esquecem de computar quanto custa a hora parada da produção, em função da necessidade de manutenção corretiva. O custo da manutenção preventiva é muito barato, quando comparado ao custo da corretiva”, compara o CEO do Grupo MH, que trabalha com construção e manutenção desde áreas civis até as de alta criticidade, envolvendo prédios industriais, subestações (transformação de alta para média tensão), cabines primárias (transformação de média para baixa tensão), equipamentos de geração de energia elétrica (geradores e usinas fotovoltaicas), painéis elétricos, nobreaks, equipamentos térmicos, de condicionamento de ar e mecânicos em geral.
Análise custo x benefício
São vários os benefícios da manutenção preventiva, mas, por outro lado, deixar de tomar esse tipo de providência pode custar caro. Entre os possíveis problemas, Aníbal Facchini destaca os riscos de parada por quebra, desgaste prematuro de peças, consumo excedente de materiais e retrabalhos.
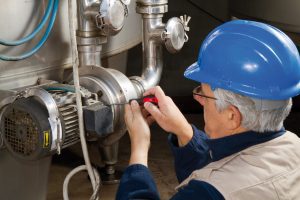
Para Eduardo Mendes, o risco de precisar fazer manutenção corretiva é o maior de todos: “Além da interrupção da produção, há os gastos excessivos com desperdício de energia e com a aquisição de materiais em regime de urgência, podendo até mesmo levar ao colapso total dos equipamentos e inviabilizar sua manutenção, sendo necessária a substituição”.
Um grande problema do mercado é que muitos empresários e administradores de negócios ainda enxergam a manutenção preventiva apenas como custo. Conforme destaca Eduardo Mendes, toda empresa que tenha alguns anos de mercado, mas nenhum programa de manutenção preventiva, provavelmente já precisou fazer manutenção corretiva. “É só olhar para o fluxo de caixa e analisar friamente os gastos realizados e que não estavam previstos. Na ocorrência de um problema, como a parada de uma linha de produção, o empresário terá alto custo adicional para restabelecer a produção, pois não teve tempo de realizar compras programadas e de negociar com fornecedores, além de não atender à produção planejada, gerando atrasos nas entregas e consequentemente afetando o faturamento da empresa e o relacionamento com os clientes. Como este custo pode ser incalculável, devemos alertar o mercado dos riscos de não realizar a manutenção preventiva”, analisa o CEO do Grupo MH.
Para Aníbal Facchini, uma maneira de modificar o pensamento que associa a manutenção preventiva apenas aos custos é medindo a ocorrência de falhas, com e sem plano de manutenção implementado. Por exemplo, o tempo do ativo disponível versus indisponível, os tempos até a ocorrência da primeira falha e o tempo entre falhas (MTTF e MTBF), comparando os custos totais envolvidos durante as paradas por falta de manutenção, versus o custo da preventiva. “O resultado desse cálculo pode ser um forte aliado na implementação das melhores práticas no segmento”, comenta.
Periodicidade adequada
É importante observar que a manutenção preventiva deve ser realizada com periodicidade compatível com a utilização e a orientação fornecida pelos integradores e fabricantes dos equipamentos. “Em sistemas de alta criticidade, se faz necessária uma análise de riscos onde a periodicidade de manutenção deverá ser definida, podendo ser até mesmo em tempo real, através de um sistema supervisório. Em casos específicos, como subestações, cabines primárias e sistemas de média e alta tensão, é recomendada a manutenção anual, onde será realizada a manutenção preventiva geral de todo o sistema e a verificação dos ensaios elétricos dos equipamentos de operação e proteção, atendendo à NR-10”, esclarece Eduardo Mendes.
Independentemente de prazos, existem alguns alertas que podem indicar que um sistema ou parte dele precisa de manutenção. Esses sinais podem ser visuais, olfativos, sonoros, térmicos, por vibrações, pela análise das grandezas elétricas e por alterações no desempenho dos equipamentos.
É preciso atenção, por exemplo, quando um equipamento apresenta variação nos resultados esperados, falhas, mau funcionamento e queda na produtividade. É importante, portanto, fazer análises comparativas dos relatórios de consumo de energia elétrica e o monitoramento em tempo real de parâmetros e efeitos físicos coletados por instrumentos de medição.
Monitoramento à distância
O mundo está em constante transformação, com destacada evolução nos campos da ciência e da tecnologia. No momento, um dos aspectos que está exigindo grande mobilização de empresas e profissionais em boa parte do planeta é a chamada Quarta Revolução Industrial.
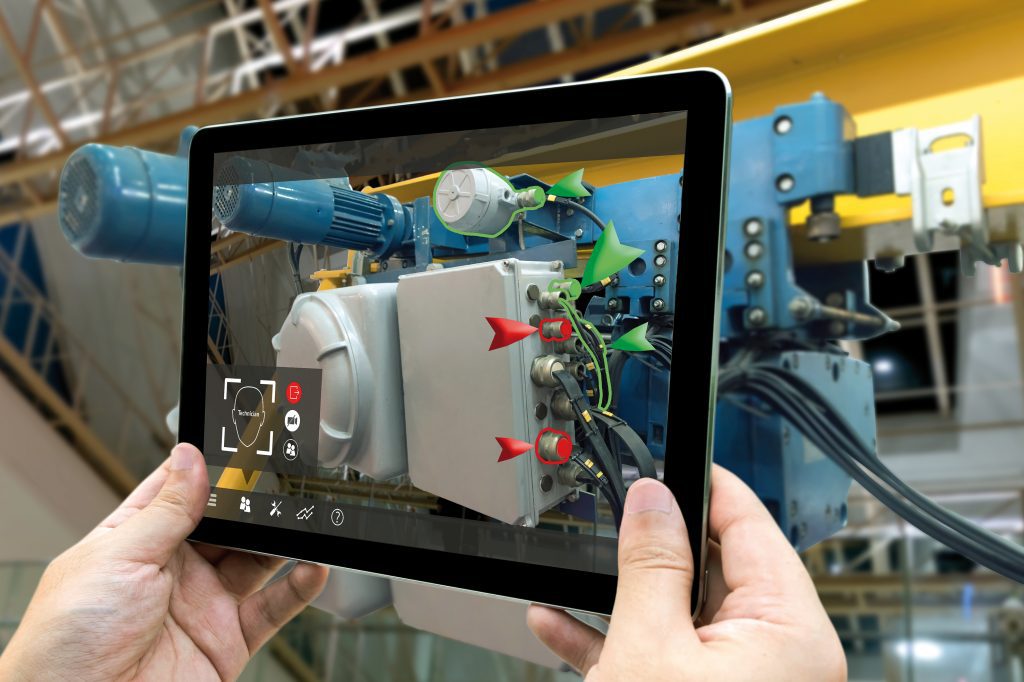
Esse fenômeno vem mudando conceitos e instituindo uma nova ordem no setor produtivo, incluindo os diversos processos a ele relacionados, como a manutenção. De acordo com Victor Fagundes, promotor Técnico em Automação da Reymaster Materiais Elétricos, a manutenção na realidade da Indústria 4.0 propõe-se a uma dinâmica completamente nova, unindo os conceitos de manutenção preventiva e preditiva à experiência de monitoramento inteligente, integrado, com acesso online e em tempo real.
Assim, prossegue o especialista, de qualquer parte do mundo uma única pessoa pode receber informações de fábricas localizadas em diferentes países, saber como estão operando e tomar as devidas decisões. “Desta maneira, a área de manutenção assume cada vez mais seu lado estratégico, buscando aumentar a produtividade nas organizações e reduzir perdas por máquinas paradas”, analisa.
Conforme exemplifica Fagundes, sistemas como o CMS 1200, da Siemens, permitem a implantação do monitoramento de condição, baseado e realizado principalmente através da análise de vibração dos componentes de máquinas e equipamentos. Podem ser monitorados todos componentes passivos de vibração, como ventiladores, bombas, agitadores, centrífugas, geradores de energia elétrica em campos eólicos, sistemas de transmissão mecânicos e caixas de redução mecânicas.
O porta-voz da Reymaster explica que através do sensoriamento/monitoramento é possível saber em tempo real se existe a iminência de falha nos componentes e a posição da ocorrência. O sistema possibilita ainda a geração de gráficos através de software integrado, que permitem o estudo da origem da falha e o comportamento da deterioração.
“Quando se identifica a deterioração, é possível estimar quando o componente irá falhar, e com base nas informações é possível agilizar a reposição de sobressalente, isso com meses de antecedência, reduzindo as paradas indesejadas de máquinas, que representam alto custo para as empresas. Diferenças de performance de componentes ou máquinas também são detectáveis, como maior consumo de energia ou até mesmo a relação com seus operadores”, completa Fagundes.
Aníbal Facchini, gerente de Produção da Full Gauge Controls, concorda que o advento da Indústria 4.0 exige mudanças também na prática da manutenção industrial, pois os sistemas estarão cada vez mais interligados, e será preciso maior controle para evitar paradas que possam afetar o desempenho dos processos.
A partir desse novo conceito de indústria, tendem a ser inseridos na manutenção novos atributos que facilitem os controles e acessos remotamente, a automação dos processos e dispositivos que permitam prever falhas previamente, como por exemplo sistemas de monitoramento à distância. “Este tipo de ferramenta possui um papel cada vez mais importante para o desenvolvimento do setor”, comenta.
Entre os produtos da Full Gauge que podem auxiliar no serviço de manutenção na área de refrigeração, por exemplo, a empresa destaca o software de gerenciamento remoto Sitrad. Com essa ferramenta, é possível acompanhar e programar períodos de manutenção de equipamentos, além de analisar dados continuamente. As informações são coletadas pelo software, que armazena os dados e envia alarmes sempre que os parâmetros não estiverem de acordo com o que foi previamente estabelecido. Com isso, se garante mais agilidade para qualquer tipo de manutenção que possa vir a ser necessária. Para ter acesso às informações é preciso apenas um dispositivo (tablet, computador ou celular) conectado à Internet. O software é de fácil operação e instalação e o download pode ser feito gratuitamente.
Por Paulo Martins
Respostas de 10
Achei muito bom este artigo.
Muito obrigado, Rafael!
A metodologia da Industria 4.0, reduz manutenção dentro das empresas. Ótima matéria.
Fizemos esta metodologia, na linha de ventilador industrial, Tivemos sucesso.
Muito obrigado, Daniel!
Boa tarde!
Saberiam me informar se já existem empresas focadas em consultoria de inovação para manutenção industrial 4.0?
Olá,
Bom dia,
Com certeza tudo isso é muito importante em um processo de gestão de manutenção, parabéns pelo conteúdo, muito bom, obrigado, abração
Ótima matéria, procuramos sempre estar alinhados nas tendências da indústria 4.0!
Oi, o meu nome é André. Achei muito legal mesmo!
Há como saber como anda (* ) a manutenção no país?
Há dados por setores produtivos e/ou por setores representativos como o da infraestrutura de transportes ( em seus modais), saúde, educação, agricultura, siderurgia, energia nos ambientes estatais, privados extratificado em pequeno, médio e grande?
* cresce, decresce ou estagnou?
Qual o número de profissionais envolvidos na atividade de manutenção?